唐澤経営コンサルティング事務所の唐澤です。中小企業診断士・ITストラテジストの資格を持ち、20年以上にわたり、中堅中小企業の経営戦略立案や業務改革、IT化構想策定などのコンサルティングに従事してきました。
このコラムでは、私のこれまでのコンサルティング経験をもとに、中堅中小企業の経営に役立つ情報を発信しています。
「日々の生産管理が煩雑で、効率が上がらない」「現場の状況をリアルタイムで把握できず、トラブル対応に追われている」
こんな悩みを抱えていませんか?中小企業が抱える生産管理の課題は、限られたリソースの中で最大限の成果を出さなければならない点にあります。そこで注目されているのが「生産管理システム」です。生産管理システムを適切に導入すれば、業務の効率化だけでなく、コスト削減や品質向上といった成果を得ることが可能です。
この記事では、生産管理システムの基本から導入のポイント、そして実際に導入を成功させた事例までをわかりやすく解説します。本記事を読めば、あなたの経営課題解決に向けた具体的な行動のヒントが得られるはずです。
生産管理システムの基本
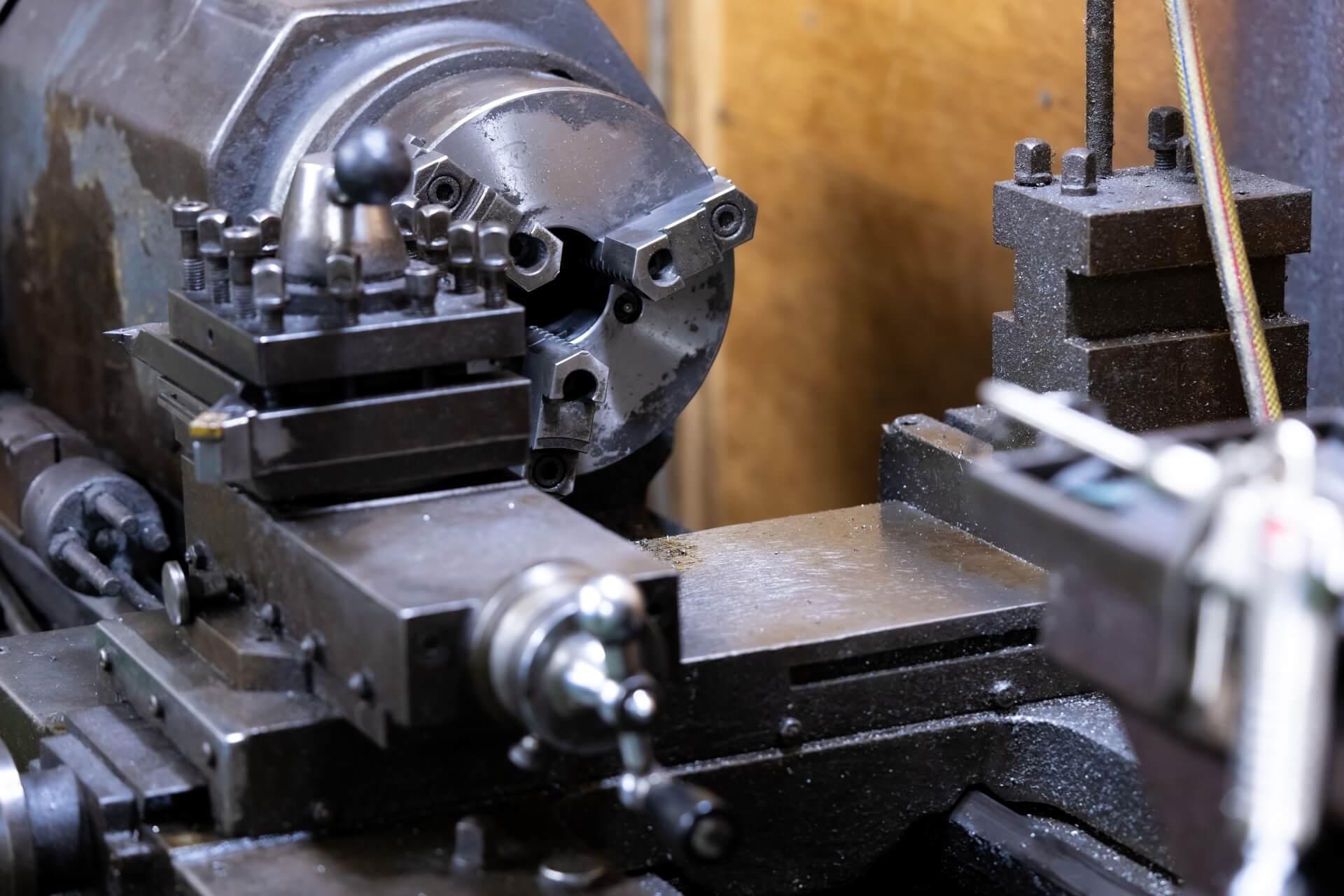
生産管理システムとは
生産管理システムは、製造業における「ヒト」「モノ」「カネ」「時間」といった経営資源を効率的に活用し、生産活動全体を最適化するためのツールです。
■システムイメージ
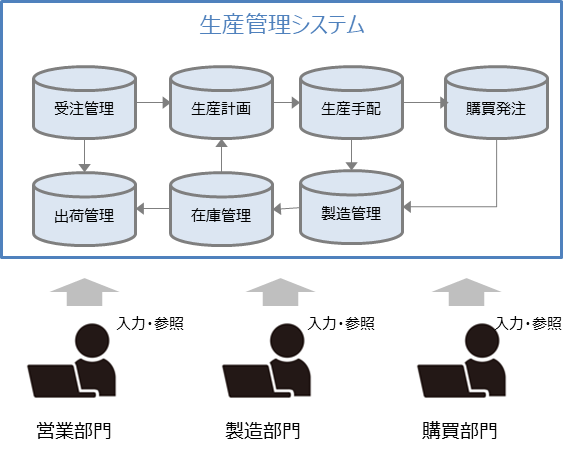
以下の主要機能を通じて、現場と経営をつなぐ役割を果たします。
- 進捗管理:作業状況をリアルタイムで把握し、計画との差異を調整する
- 在庫管理:過剰在庫や欠品を防ぎ、必要なリソースを適切に確保する
- 原価管理:正確なコスト把握により、収益性を向上する
- 余力管理:生産リソースの使用状況を見える化し、負荷を最適化する
生産管理システムの役割
生産管理システムが果たす役割は、現場の透明性を高めるとともに、リソースを最適化することにあります。
以下の3つが代表的な役割です。
- リアルタイムでの進捗・余力の把握:進捗状況だけでなく、余力(人員、機械稼働状況など)を同時に管理することで、生産スケジュールを柔軟に調整可能です。これにより、無理のない生産計画が実現します。
- 在庫と生産の調整:在庫情報をもとに、無駄のない生産量を確保します。たとえば、需要変動に応じて余力を活用しながら、迅速に対応する仕組みを構築することで、顧客満足度を向上させることができます。
- データに基づくボトルネックの解消:作業負荷や稼働率を分析することで、リソースの偏りやボトルネックを特定し、計画的な改善が可能になります。
生産管理システムがもたらすメリット
生産管理システムが提供するメリットは以下の通りです。
- リソースの最適活用:必要以上や不足がないようにリソースを調整することで、効率よく運用が可能になります。
- 稼働率の向上:無駄な稼働や作業の停止を減らし、設備や人員の稼働率を高めます。
- 問題の早期発見と対策:リソースが不足したり、計画が過剰(オーバーロード)になった場合でも、すぐに問題を見つけ、迅速に対応できます。
- 全体的な生産性向上:リソースの配分が効率的に行えるため、工場全体やチーム全体の生産性が向上します。
これらの機能を活用することで、中小企業でも限られたリソースを最大限に活かし、効率的な生産体制と顧客満足度の向上が実現可能となります。
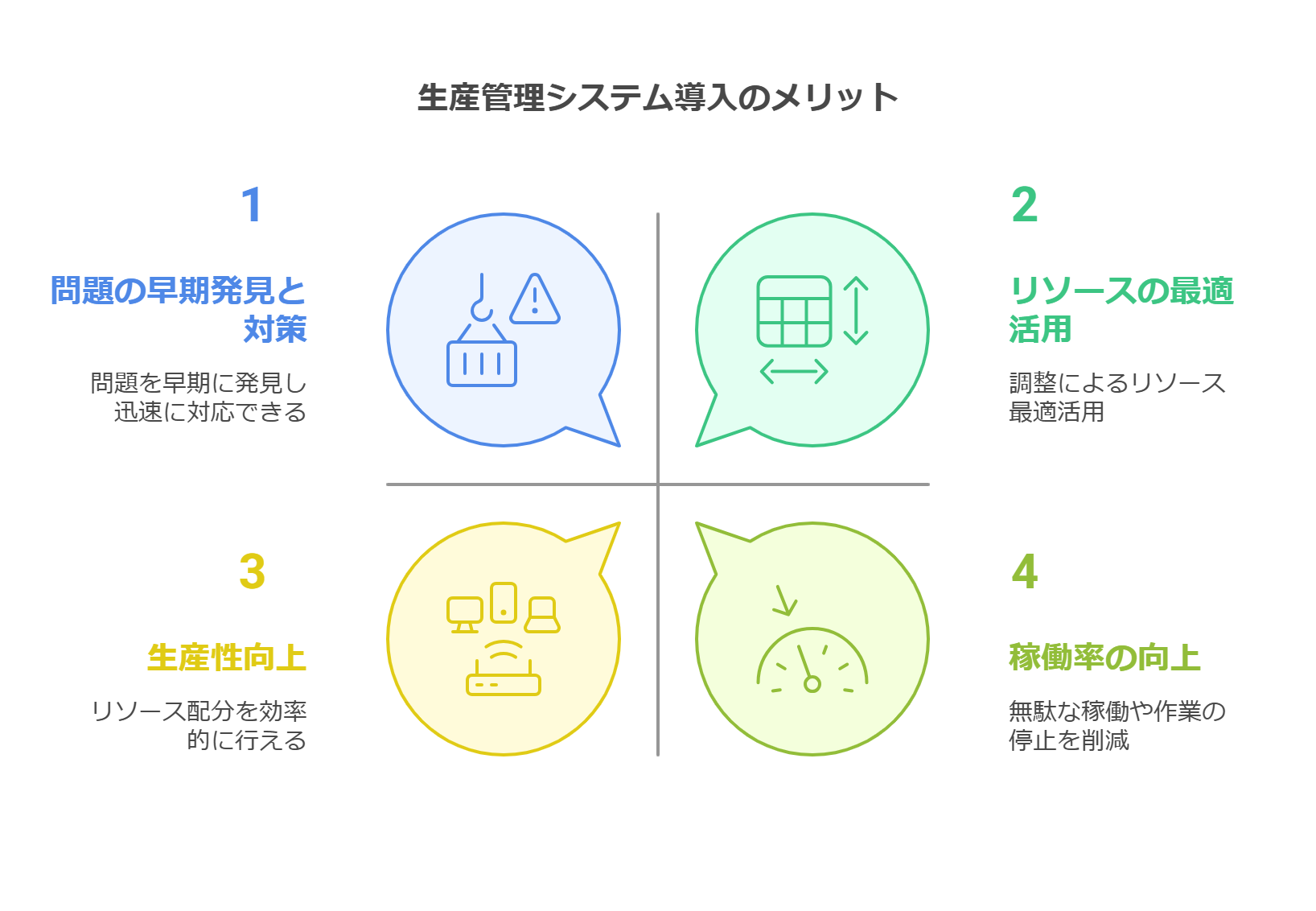
生産管理システム導入のポイント
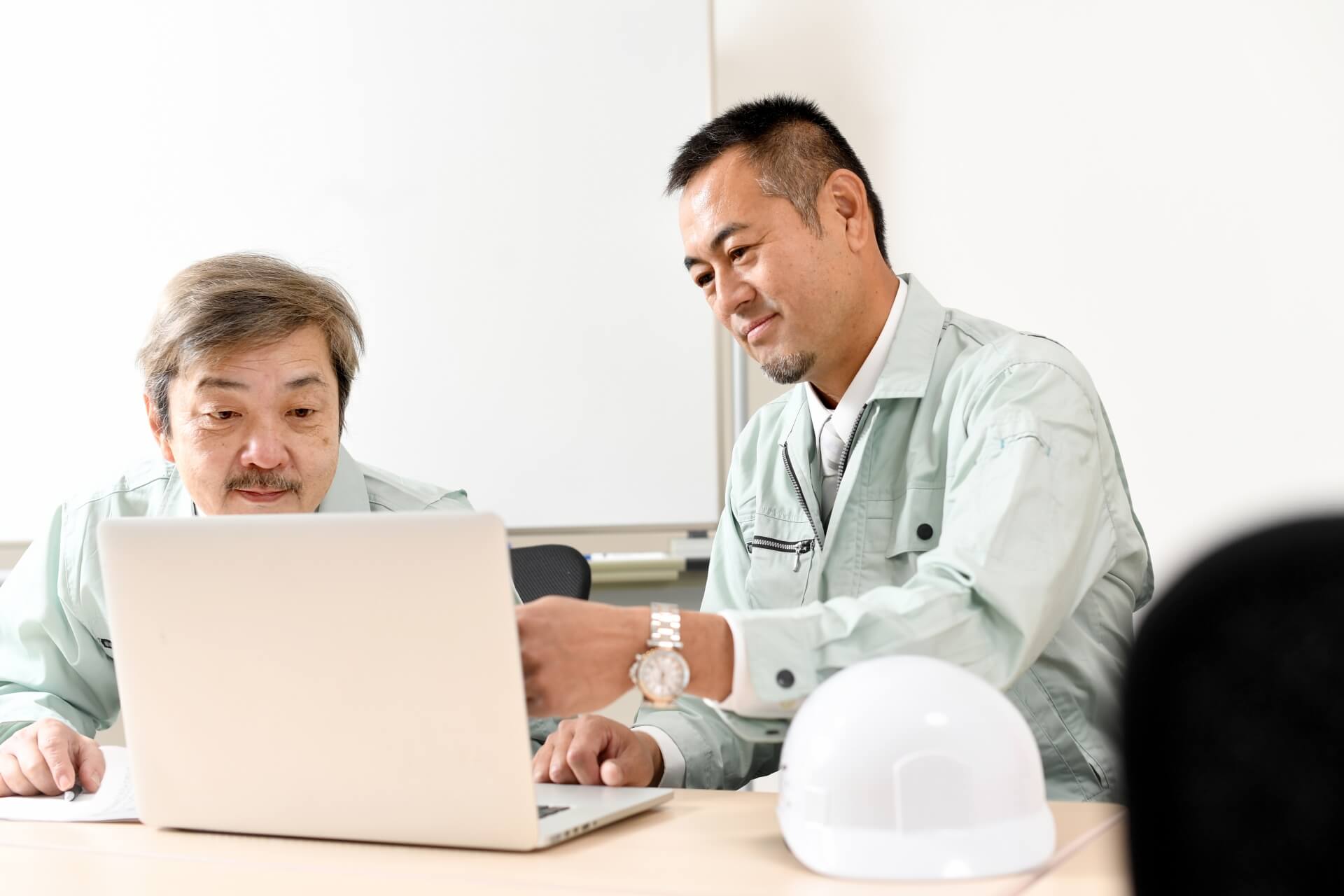
導入前に知るべき重要な視点
生産管理システムの導入で失敗する原因の多くは、システム選定時の視点が「機能」や「価格」だけに偏ってしまい、自社の特性を十分に考慮しないことです。
特に中小企業では、現場の実態を反映しないシステムが現場で使いこなされないケースが散見されます。
導入を成功させるためには、以下の3つの視点で準備を進めることが重要です。
- 自社の「生産形態」を明確にする:受注生産型なのか、見込み生産型なのか、それともその混合型なのか等、生産形態によって求められる機能が大きく変わります。例えば、受注生産型であれば、個別案件ごとの原価管理や余力のリアルタイム把握が重要になりますが、見込み生産型では需要予測や在庫の適正化がより優先されます。
- 「製造プロセス」の特性を把握する:自社が行う製造が組み立て型なのか、プロセス型(化学品や食品など)、またはプロジェクト型(造船や建築など)なのかによって、システムに求める機能が変わります。例えば、プロセス型では品質管理機能やトレーサビリティが不可欠ですが、組み立て型では部品表(BOM)や工程進捗の管理が重視されます。
- 現場の運用フローを見直す:現場でどのような業務が行われ、どの部分にボトルネックがあるのかを洗い出すことが必要です。進捗管理や在庫管理に問題があるのか、それとも人的リソースの偏りが課題なのかを明確にし、その課題に対応できるシステムを選定することが重要です。
選定の際に重視すべき要素
生産管理システムを選ぶ際、単に「使いやすい」や「高機能」なものを選ぶのではなく、以下の具体的な要素を基準に評価する必要があります。
- 対応可能な生産形態とプロセス:生産管理のパッケージシステムは、多くの場合、特定の業種や生産形態に特化しています。自社の生産形態やプロセスに完全に一致するものを選ぶか、もしどうしても適合できない部分があるのであれば、必要に応じてカスタマイズができるパッケージシステムを選ぶべきです。
- 余力管理と進捗管理の精度:生産性向上の鍵となるのは、現場の稼働率や余力をリアルタイムで正確に把握することです。設備や人員の余剰や不足を即座に確認し、計画の調整ができる機能が不可欠です。これにより、無理のない生産スケジュールを構築できます。
- 在庫と生産の連携:在庫管理は生産管理の中心的な課題です。適正在庫を維持しながら、過剰在庫や欠品を防ぐシステムが必要です。特に、見込み生産型では需要予測と生産スケジュールが緊密に連携する仕組みが重要です。
- 運用のシンプルさと現場の受容性:中小企業では、現場スタッフのITリテラシーが高くない場合が多いです。そのため、複雑なシステムよりも、現場スタッフが簡単に使いこなせるインターフェースが求められます。
- 将来の拡張性:現在の業務に対応するだけでなく、今後の事業成長や製品ライン拡張に対応可能なシステムを選ぶことが重要です。カスタマイズ性やモジュール追加の柔軟性があるかを確認してください。
成功する導入プロセス
生産管理システムの導入を成功させるには、計画的なプロセスが必要です。
以下の3つのステップを参考にしてください。
- 現場の課題を徹底的に分析する:導入前に、現場のどの業務や管理に課題があるかをしっかりと洗い出します。たとえば、「生産の進捗状況が見えない」「在庫が過剰になりがち」等の具体的な問題を把握します。
- 段階的な導入を行う:一度に全ての機能を導入・活用しようとせず、まずは進捗管理や在庫管理など、課題が顕在化している領域に限定してトライアル運用を実施します。例えば、特定の製造ラインだけでシステムを試験導入し、作業負荷やリードタイムのデータを取得。その結果を基に、設定や運用手順を調整します。このプロセスを通じて、現場でのフィードバックを反映させながら段階的に機能を拡張し、不具合の早期発見と解決を図ることができます。
- 導入後のサポート体制を確認する:システム導入後、現場での運用がスムーズに進むよう、ベンダーのサポート体制を確認しておくことが重要です。特に中小企業では、自社に専任のIT担当者がいない場合が多いため、導入後のサポートが事実上の命綱となります。
生産管理システムの選定と導入には、自社の生産形態・製造プロセスを正確に理解し、現場の課題に対応する具体的な機能を重視することが必要です。
さらに、段階的な導入と現場スタッフの関与を通じて、運用後に真の効果を引き出せる仕組みを構築しましょう。
私の体験談
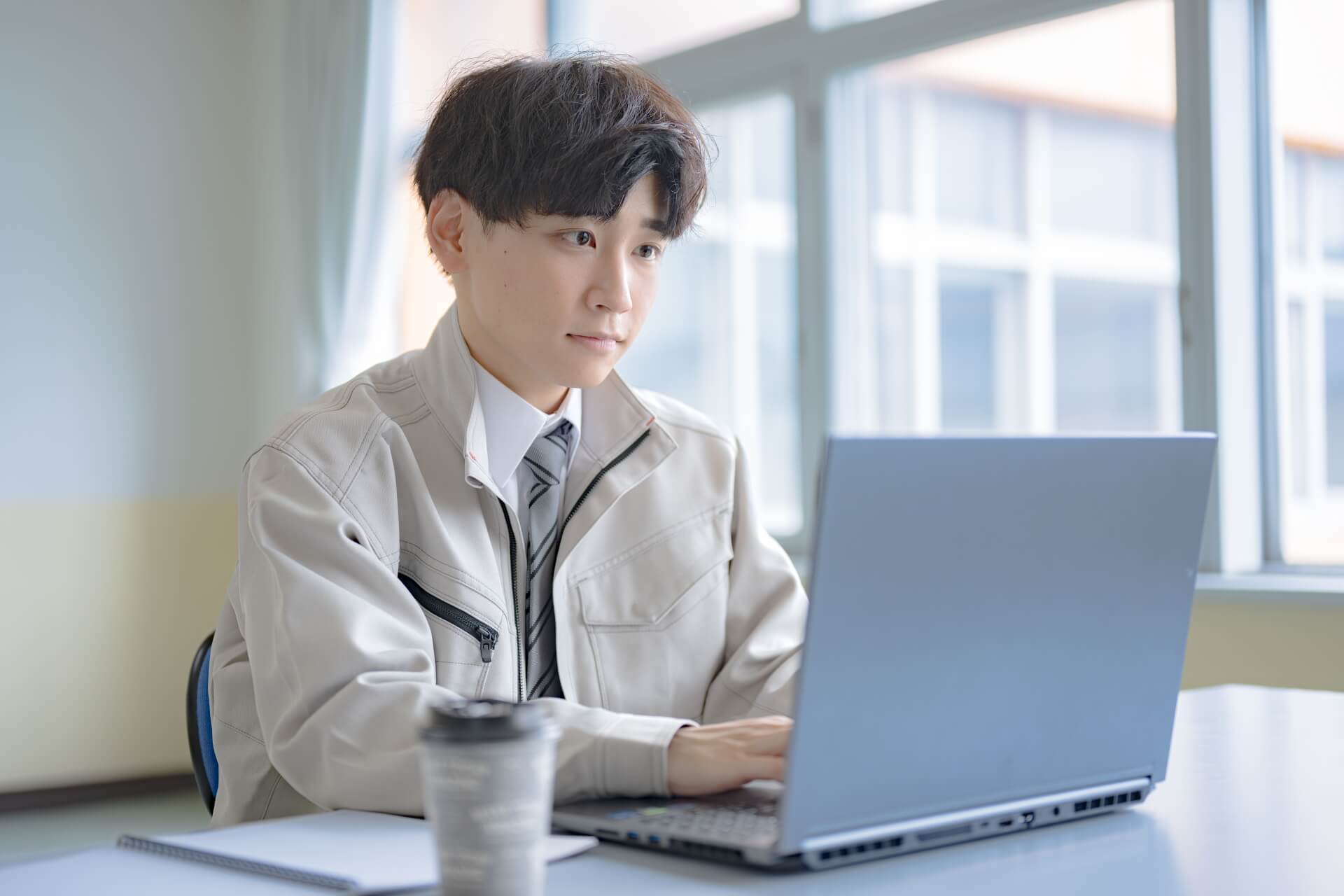
私が支援したある企業は、祖業が卸売業でありながら、顧客の要望に応えて加工業務を始めた結果、製造業へと業態を拡大しました。
製品は既製品と特注品があり、従業員数は約200名以上の中小企業でしたが、以下の課題が顕在化していました。
- 生産進捗が見えない:特注品の工程進捗が不明瞭で、納期遅延が頻発。
- 原価管理が不十分:製品別の収益性が把握できず、不採算製品が利益を圧迫。
- 資材発注が手作業:既製品の部品発注が非効率で、在庫過剰が発生。
以上の課題を踏まえ、現状利用している販売管理システムから生産管理システムへの全面移行により、生産管理体制を整備することを提案しました。
その中核にはMRP(資材所要量計画)の導入を据えました。
MRPとは、製品に必要な部品や材料を計算し、適切なタイミングでの発注を支援する仕組みです。この運用のために品目マスタとBOM(部品表)を整備し、データの正確性を高めました。
また、進捗管理機能を導入し、特注品の製造状況をリアルタイムで把握できるようにしました。
さらに、原価管理機能の活用により、製品別の利益率をデータで明確化し、収益改善を支援しました。
生産管理システム導入により、以下の成果が得られました。
- 進捗の可視化:納期遵守率が10%以上向上し、顧客満足度が改善。
- 原価管理の強化:不採算製品の特定と価格見直しを実施し、利益率が12%向上。
- 資材発注の効率化:MRPの活用で発注ミスが減少し、業務が効率化。
このプロジェクトを通じて、生産管理システムの効果を改めて実感しました。それは次の3点に集約されます。
- 経営と現場の一体化:データの正確性が向上し、経営層が現場の状況をリアルタイムで把握できるようになりました。これにより、戦略的な意思決定がスムーズになりました。
- 現場の効率化と負担軽減:手作業での資材調達管理や属人的な工程管理が減り、現場スタッフの負担が大幅に軽減しました。これにより、生産性向上とモチベーションアップが実現しました。
- 収益改善の基盤構築:原価管理のデータを基に利益率を高める施策を実行。これが収益性向上に直結し、企業全体の競争力を強化しました。
Q&A
Q1: 生産管理システムを導入する際に、導入費用が高くて不安です。どうすればいいですか?
A: 生産管理システムの導入費用は、選定するシステムの規模や機能によって異なりますが、費用対効果を十分考慮することが重要です。
中小企業では、最初からフル機能を導入するのではなく、段階的に導入することで初期費用を抑えることができます。
また、クラウド型のサブスクリプションモデルを採用しているシステムは、初期投資を抑えつつ必要に応じて機能を拡張できます。
まずはトライアル期間を活用して、自社の業務に適しているかを確認してから導入を検討してください。
Q2: 現場スタッフがITに不慣れで、生産管理システム導入に抵抗があります。どうしたら良いでしょうか?
A: 現場スタッフがシステムを使いこなせないと、どんなに優れたシステムでも効果を発揮できません。そのため、以下のステップを踏むことをお勧めします。
・シンプルな機能からスタート:最初は基本的な機能だけに絞り込み、複雑な操作を避けることで、現場の負担を軽減します。
・段階的なトレーニング;現場スタッフに対して、実務に即したトレーニングを段階的に行います。特に、進捗管理や在庫管理など、日常業務に直結する部分から教育を始めると効果的です。
・導入後のフォロー体制:運用開始後も、現場スタッフからの質問や困りごとに対応できるフォロー体制を整え、安心してシステムを使える環境を提供します。
Q3: 自社に合った生産管理システムの選び方がわかりません。
A: 生産管理システムの選定では、以下のポイントを考慮すると良いでしょう。
・生産形態と製造プロセスに合致しているか:自社の生産形態(受注生産・見込み生産など)や製造プロセス(組み立て型・プロセス型など)に適したシステムを選びます。
・必要な機能が過不足なく備わっているか:現場の課題を解決するのに必要な機能があるかを確認します。進捗管理、在庫管理、余力管理など、自社の優先課題を明確にしましょう。
・拡張性があるか:将来的な事業の成長に対応できる柔軟性があるかを確認してください。
不明点があれば、ベンダーに具体的な事例やデモを依頼することで、より明確な判断が可能になります。
Q4: 導入後、現場でうまく使われない場合はどうしたら良いですか?
A: システムが現場で使われない理由の多くは、「現場での運用が難しい」「システムの導入目的が共有されていない」ことにあります。
次のようなアプローチで改善を図ることができます。
・現場の声を聞く:導入初期に現場スタッフからの意見や要望を収集し、運用方法やシステム設定を調整します。
・目的を共有する:システム導入によって「現場の負担が軽減される」「トラブル対応が迅速化される」など、具体的なメリットをスタッフに伝えます。
・運用フローを簡素化する;システムが煩雑すぎる場合は、操作を簡略化し、負担を軽減する設定変更を行います。
まとめ
生産管理システムは、企業の生産効率や収益性を向上させる強力なツールです。
ただし、その導入を成功させるためには、しっかりとした準備と段階的なアプローチが必要です。
本記事で解説したポイントを振り返り、導入の成功に必要な要素を再確認しましょう。
1. 現場の課題を抽出する:
導入前に、現場での具体的な課題を徹底的に洗い出します。例えば、以下のような問題がどこに存在するかを明確にします。
・生産の進捗が見えず、納期遅延が発生している。
・在庫が過剰または不足しており、資金繰りや生産効率が悪化している。
・属人的な管理に依存しており、トラブルが発生しやすい。
これらの課題を明確化することで、導入すべきシステムの必要な機能が自ずと見えてきます。
2. 自社の特性を理解する:
自社の生産形態(受注生産・見込み生産・混合型)や製造プロセス(組み立て型・プロセス型など)を正確に把握します。それに基づき、システム選定の基準を定めましょう。
3. 現場との連携を強化する:
現場の意見を反映し、現実的で使いやすいシステムを選定しましょう。また、トライアル運用を活用し、現場からのフィードバックを基に調整を行うことも重要です。現場と経営が一体となり、生産管理システムを「使われるツール」にすることが成功のカギとなります。
4. 段階的に導入を進める:
最初から全ての機能を導入しようとせず、優先度の高い課題を解決する機能から始めることが有効です。進捗管理や在庫管理といった基本機能を優先し、運用が安定してから余力管理や原価管理などの高度な機能を追加しましょう。
5. 導入後の改善を続ける:
システムの運用を開始した後も、現場の運用状況をモニタリングし、必要に応じて設定を調整します。データを活用して継続的に業務フローを最適化し、システムが企業全体の成長を支える基盤となるよう進化させてください。
生産管理システムは、適切に導入することで企業の競争力を飛躍的に高めるツールです。
本記事を参考に、一歩ずつ確実に準備を進め、現場と経営をつなぐ仕組みを構築してください。
DXの具体的な進め方やツール選定、社内体制づくりなど、お悩みやご不明点がありましたらお気軽にご相談ください。唐澤経営コンサルティング事務所では、中小企業診断士・ITストラテジストとして、中堅中小企業の規模や業種に合わせた最適なアドバイスとサポートを行っています。
お問い合わせや無料相談は、以下のフォームからお願いいたします。
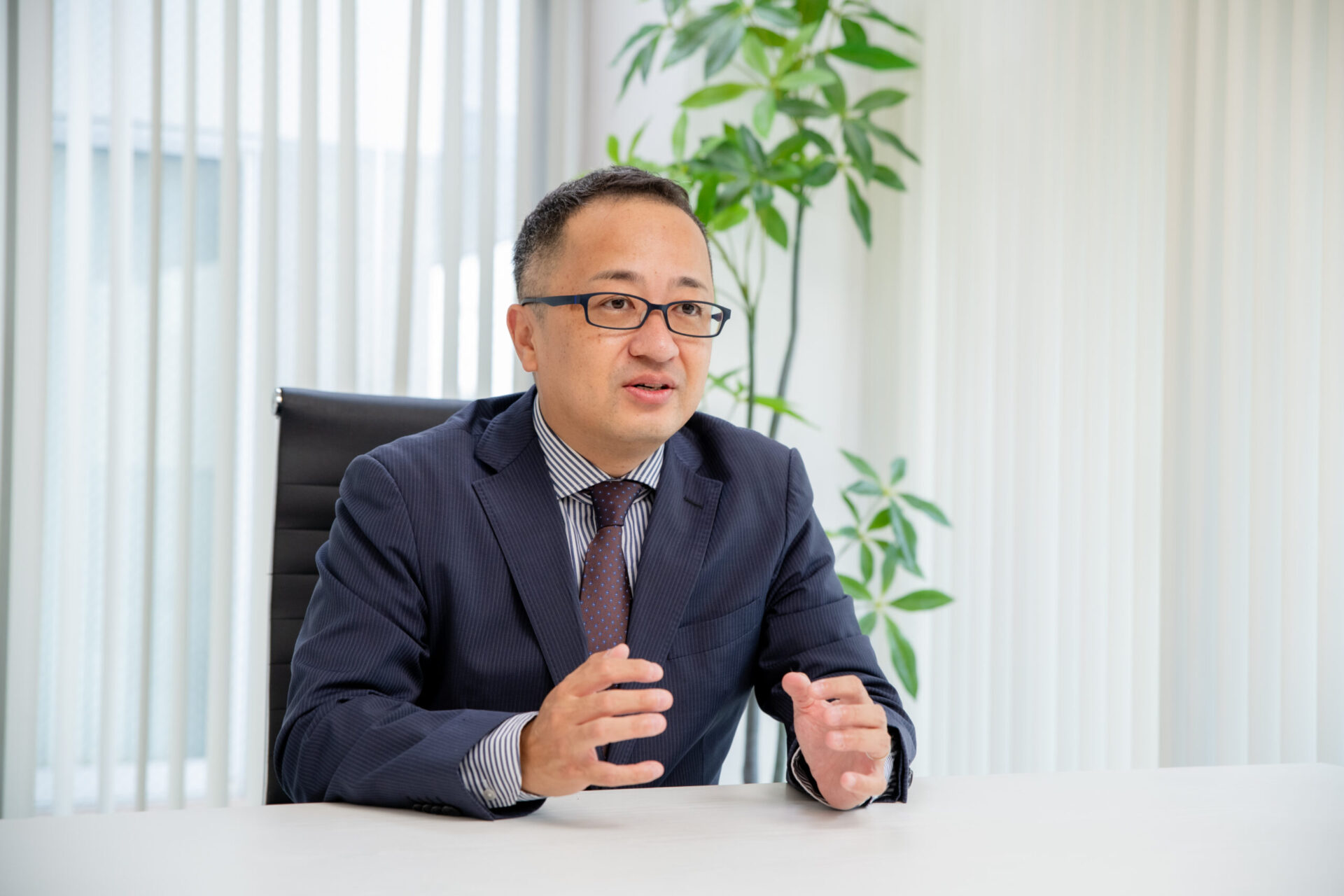
経営者が抱える経営課題に関する
分からないこと、困っていること、まずはお気軽にご相談ください。
ご相談・ご質問・ご意見・事業提携・取材なども承ります。
初回のご相談は1時間無料です。
LINE・メールフォームはお好みの方でどうぞ(24時間受付中)